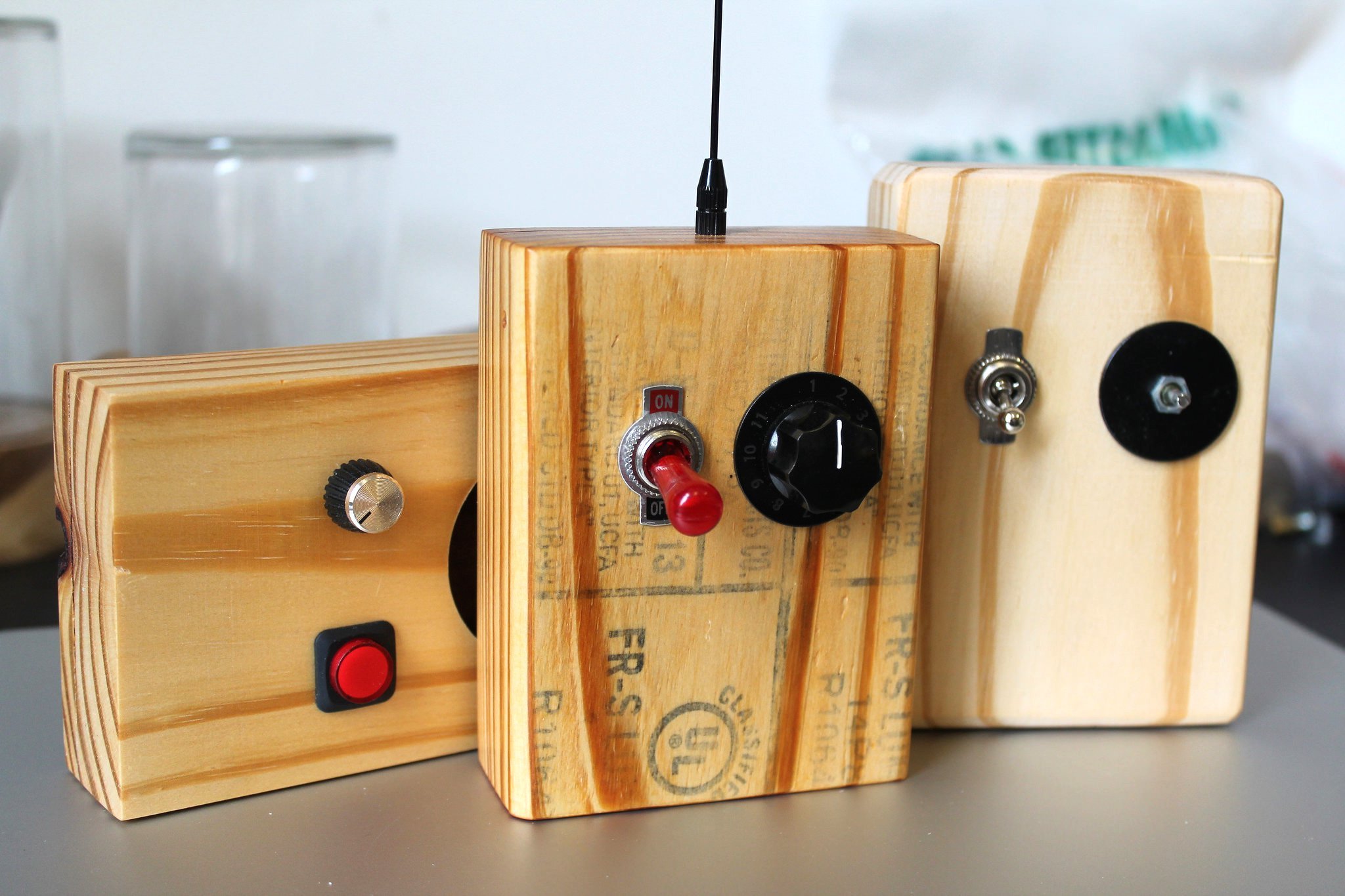
As laser cutters offer a wide range of benefits when working with wood, it is clear that they are an excellent choice for many projects. The ability to create intricate designs with ease, combined with the ability to also engrave and cut in the same production cycle, makes laser cutters a highly efficient prototyping solution. The low cost of wood and the ease of which it can be machined also make it an ideal material for those looking to scale their designs from prototypes to full-scale production runs.
However, like all other manufacturing processes, laser cutters are not without their faults, and mistakes can creep into a design if not properly planned. By avoiding these four common mistakes, engineers can help to reduce the cost of their projects, improve their designs, and ensure a high degree of precision and accuracy in their parts.
Mistakes To Avoid When Laser Cutting Wood
Mistake Number 1 – Attempting Small Mechanical Details
When it comes to mechanical designs, it is often the case that a prototype will require some degree of precision, especially when creating parts that will eventually be mass produced. However, trying to achieve the same degree of precision with laser-cut wood can lead to major headaches, and in many cases, significant design mistakes.
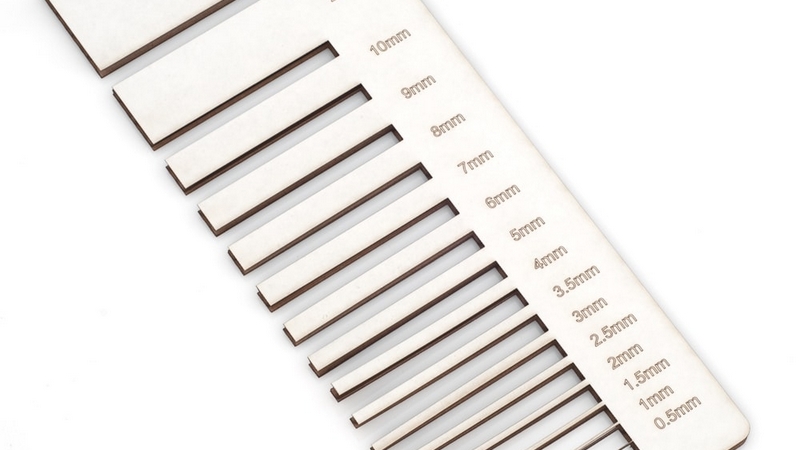
Because of the granulated nature of wood, trying to create fine mechanical details is arguably one of the biggest mistakes an engineer can mak. The large grain structure of wood also means that small parts, such as cogs and teeth, cannot be reliably cut and will likely chip away.
This doesn’t mean that wood can’t be used in mechanical designs, especially those that are not being mass produced, but it does mean that wood should not be used for parts that require a high degree of precision. Instead, engineers should turn to materials such as plastic and metal that not only offer greater precision but are also stronger.
Mistake Number 2 – Expecting Any Wood Finish
When it comes to laser-cut wood, it is essential that engineers understand the differences between naturally sourced wood and our engineered wood products. One of the biggest differences by far is that naturally sourced wood is available in a wide range of types, including oak, ash, and birch, whereas wood suitable for laser cutting are limited to specific types such as maple and walnut (due to the release of harmful compounds from other woods during the cutting process).
Another major difference between naturally sourced wood and our engineered wood is that naturally sourced wood has unique characteristics such as colour variations, knots, and grain patterns. While these can be aesthetically pleasing, they also introduce challenges during manufacturing stages. For example, trying to cut a specific pattern in wood with a laser cutter can be challenging when the wood itself is unpredictable (i.e. knots may cause pieces of the part to fall out).
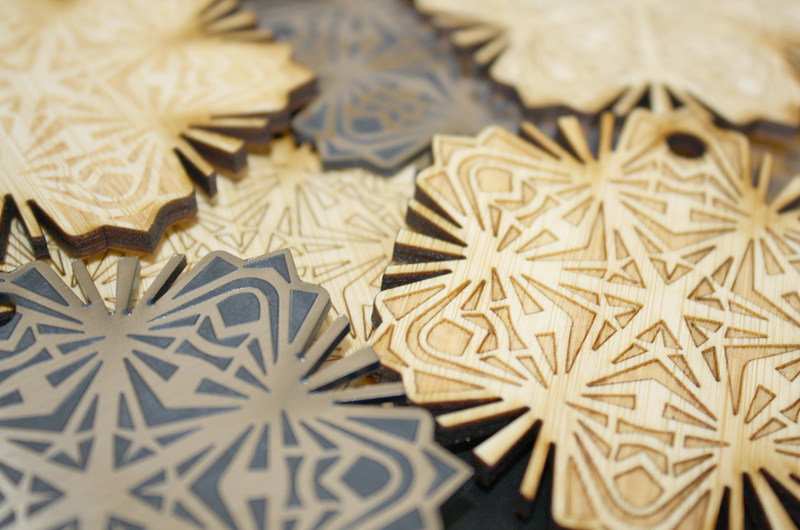
Our engineered wood, however, is manufactured to be highly consistent, meaning that the colour, texture, and grain are uniform throughout the material. This consistency also means that laser-cut parts made from engineered wood will exhibit little variation, and the precision and accuracy of Ponoko laser cutters ensure that each part is production-grade.
Mistake Number 3 – Burned Edges
When laser cutting wood, the high-intensity beam of light vaporises the material, resulting in a clean cut. This is ideal when cutting materials such as plastic and metal as these materials do not discolour or melt when exposed to intense heat.
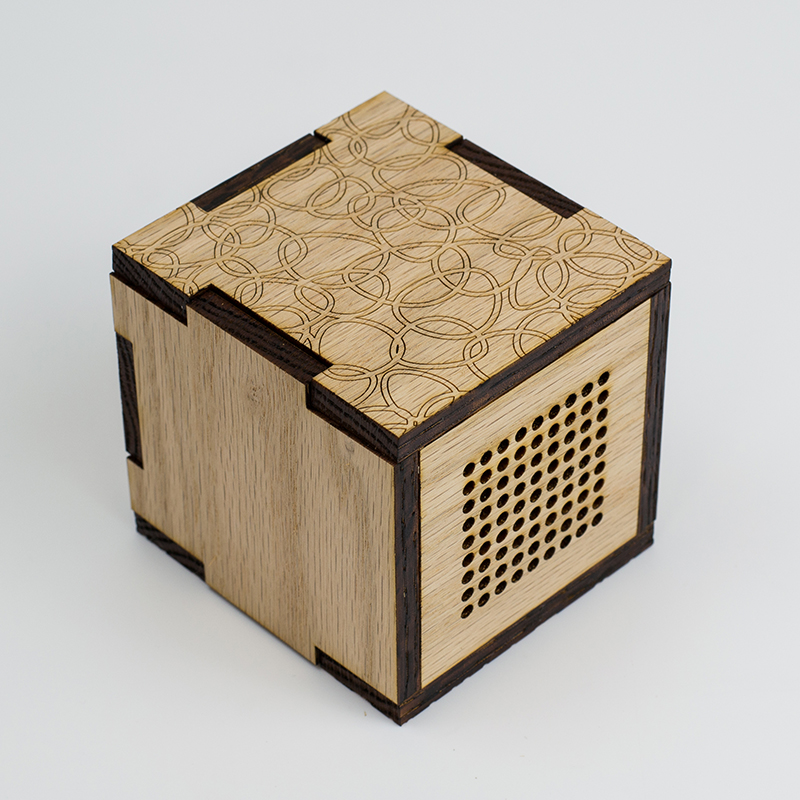
However, wood reacts very differently to heat, and as such, laser-cut wood edges have a charred appearance. While this can be used to add an aesthetically pleasing touch to a design, it may not always be what is desired. Unfortunately, there is no way of getting around the burned edge when laser cutting wood, meaning that engineers should be aware of this effect before committing to laser-cut wood parts.
Mistake 4 – Engraving Damage
When it comes to laser-cut wood, engraving is an excellent option due to the high contrast resulting from laser charring. The carbonisation process of wood under extreme heat results in all woods having a deep black colour, and this stands out on all kinds of woods whether it is oak, birch, or ash.
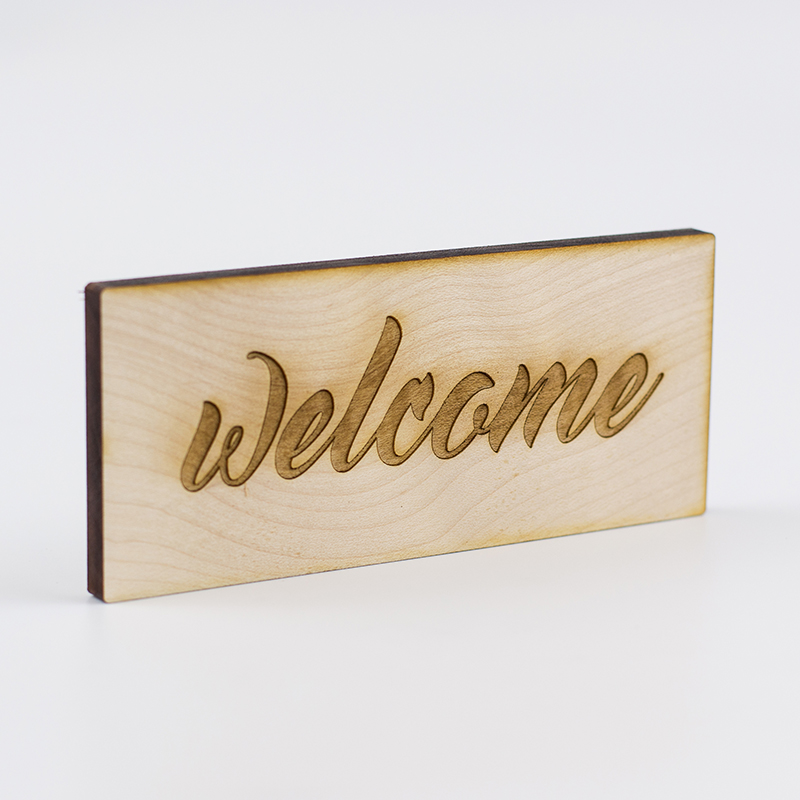
However, the discolouration of the surrounding area can give engraved designs a somewhat washed-out appearance, as if the laser cutter had accidentally wandered off course. Unfortunately, there is very little that can be done to prevent this discoloration, meaning that those looking to engrave large areas need to take this into consideration.
As such, engraved designs are typically ideal for graphics, logos, and text as opposed to art and other designs that rely on colour.
Tips For Laser Cutting
Avoid Engraving Large Areas
Laser cutting wood is an excellent option for both prototyping and mass production thanks to its extremely low cost and ease of manufacturing. However, large engraving areas, such as large images, should be avoided as this can result in heat damage to the wood.
Recognise laser kerf
Despite what we may see in sci-fi films, all lasers naturally diverge as they travel away from their source, resulting in a widening of the beam width. In the case of laser cutting, this “laser kerf” will result in a slightly wider cutting width on the underside of the part compared to the top side. Thus, when getting parts laser cut, make sure to keep this kerf in mind, and remember, the kerf itself is a function of part thickness, with thicker parts being more susceptible.
Use wood for prototyping
Wood is an excellent material for prototyping as it is extremely cheap, and the charred edges of laser-cut wood can also make it aesthetically pleasing. However, it is important to recognise that charred edges can only go so far, and plastic and metal will offer better mechanical properties. This means that wood should only be used in designs where such mechanical properties are not essential, such as enclosures that need to have a natural look.
Use vector graphics
Finally, when designing laser-cut wood parts, it is essential that vector graphics are used. Unlike raster graphics, vector graphics describe the path that the laser head needs to make, and this results in extremely high-quality wood parts. The use of vector graphics also means that designs can be scaled without the need for raster graphics, and this helps to reduce the cost of the final part.
Key Takeaways
- Wood is great for prototyping, but metals and plastic ofter far superior with regards to longevity, resistance to environmental conditions, and strength
- Laser-cut wood will discolour due to the high-intensity energy from the laser beam
- This discolouration can be asthetically pleasing, depending on the design
When taking advantage of laser-cut wood, it is essential to recognise that the mechanical properties offered by plastics and metal cannot be matched. While laser-cut wood is ideal for prototyping, it can also be used in the final stages of a product.
However, when using laser-cut wood in a production environment, it is crucial to also recognise that laser cutting wood will always result in discolouration of the wood. The high-intensity light from the laser beam causes a burning effect that changes the colour of the wood, and this cannot be avoided.
Despite this discolouration, laser-cut wood remains strong and structurally sound, making it ideal for use in enclosures, boxes, and other prototyping applications. The versatility of laser-cut wood extends beyond its ability to be used in prototypes; its ability to be engraved and sanded makes it ideal for use in decorative pieces and high-quality products.
Overall, laser-cut wood is an exceptional material that offers engineers a multitude of benefits, and the numerous mechanical and aesthetic possibilities make it a material that will continue to grow in popularity.